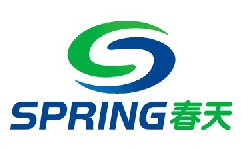
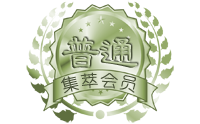
福建省格林春天新材料股份有限公司 | |
联系人: | 林国良 总经理 |
手机: | 13806045776 |
电话: | 86-0592-7119133 |
传真: | |
Q Q : | |
Email: | springink@yahoo.com.cn |
地址: | 中国福建厦门市高新区创业园创业大厦101-102单元 |
商铺: | http://waterbasedink.ccedwy.com/ |
凹版油墨经常出现的问题
1.糊版(埋版、堵版) 凹版油墨故障现象:印品图文或小字印不出来,甚至于印品上有一层墨迹,而图案模糊。 原因:①油墨干燥速度太快,使油墨干结在网纹网穴内。或者图案网穴早被干结块堵住,新墨上去不能完全复溶,成大面积堆在印品上,涂花图案文字;印刷机速度太慢,刮刀除去非图纹部分油墨后,在到达压印点前,墨已成干固态不转移。凹印网穴中的墨一般转移率为1/2,也就是说还有1/2留在印版上,油墨粘度大,干得快,即使辊筒再复入墨斗中,也很难全部溶解,这样反复多次,油墨转移率下降,最终变成堵版。②印版腐蚀得太残或网点不清晰。凹版是腐蚀铜面后经镀铬抛光而得的。腐蚀达不到要求,深度不够,网穴孔内壁不光滑,呈毛茸茸状态,镀铬又厚,铬块已填满网穴,抛光不好发生毛刺,都可以促使墨层很快干固,造成堵版。油墨因保管不好而结皮,印刷中的纸块,塑料屑以及周围尘埃因静电吸附入墨中,或直接落在印版网穴中,也能造成糊版;印刷过程中停机,残留在版面上的皮膜尚未及时清理,逐渐堆积,将网点糊住;油墨流动性不良,不同种、不相溶的墨掺入,溶剂误用,油墨中真溶剂数量少了,造成复溶性差,粘度又大,不易将非图纹部分刮净,特别是网点边缘残留干结,不断扩展,清洗不及时,致使网点被埋住。 解决办法:主要是根据机器速度,即刮刀刮墨后在印压点所经历的时间,使用溶剂调节其干燥速度,尽量减缓干燥速度。按下列时间考虑。 高速单元式轮转凹印机:0.02~0.1s 中、低速轮转凹印机:0.04~0.15s 高速单张平台凹印机:0.1~0.2s 低速单张凹印机:0.5~0.6s 油墨中可调入挥发较慢的溶剂,如沸点在120~150℃的、蒸发潜热较大的溶剂;当油墨干燥速度较快时,可适当提高印刷速度。使刮除非图文部分墨后,趁网点中的墨流变尚好尚未干时即行压印;检查版子腐蚀、镀铬、抛光的质量是否合适。一般情况下,在其他条件都认为合适的情况下,发生糊版,擦洗一次后,如果不久又发生糊版,并从图文上可以看到层次不协调,则可认定为印版所造成,这时,要重新制版;检查吹风、加热装置,是否因方向变动,吹到了版面上。若是则要立即纠正;对墨中混入的渣子、版上的异物要及时清除,对有循环泵的印刷设置,可在出口置120目的钢丝网过滤之;油墨粘度应根据速度愈快、需要粘度愈低的原则,进行调整。但也要防止矫枉过正。一般凹印油墨粘度掌握在19~ 25s/25℃(4号粘度杯)范围即可。 为了保证油墨复溶性,应根据油墨制造厂的意见,保证或增加该墨中的真溶剂量。同时,不同溶剂类型、不同用途的油墨不要互掺,防止树脂析出,丧失墨性。 2.咬色 故障现象:在卫星式轮转凹印机或单元组合式轮转凹印机上进行套色印刷中,特别是印刷聚烯烃薄膜时,第二色油墨将前一色印刷的墨迹粘拉掉了。 原因:由于前一色的油墨彻干性慢了,或对被印体粘附性不强,而后一色(即第二色附着性太大、印刷压力太大或油墨中树脂量太少,都可以将前一色印迹咬掉;印刷速度太快,前一色未干,经受不了第二色的分裂力,同时,印刷时吹风没有集中在图案上或风量小了,调整时,在第一色中,慢干成分的溶剂太多,使前一色不能按要求粘附、干燥而受第二色的粘拉破坏。 解决办法:针对前一色,应该加快干燥性,加入低沸点溶剂;减慢速度;增加树脂量,加入带树脂的调墨液,不要用纯溶剂;给风管堵塞部分疏通,使风集中吹过印刷图案的表面;因粘度大而调整时,慢干成分太多了,则应以原墨补救。 针对第二色,应调整版辊与压印辊的距离以减少压力;第二色的粘度应比第一色稍小一些。 同步减慢速度。若系前一色对被印刷体附粘不牢,则应检查对薄膜的处理是否在38dy/cm以上,否则应重新处理,或在油墨中加入含树脂的溶液,如冲淡剂。 3.粘脏(粘页) 故障现象:在卷筒(纸,塑料或箔)印刷后,收卷收集(堆,卷)中,印品图案的一部分或全部图影粘贴在相附的印张背面,也叫粘贴或反印;一种是在收成卷堆放过程中,印品互相粘在一起,印迹沾背造成废品,也叫堆积污脏。不管是印刷中,还是印刷完成堆放中,都叫收卷粘连。 原因:主要是油墨的残余粘性所致。造成这种状况的原因,是大量的残留溶剂的存在,这种溶剂往往是高沸点的,印刷过程中,不易挥发出去,印刷品收卷时,油墨中树脂还未凝固,从而产生残余粘性。 另外,许多材料中含增塑剂比较多,它在一定的条件下,可以膨润油墨中的树脂从而造成粘脏。 解决方法;提高油墨的初干性和彻干性,加强吹风和热量,使墨膜干燥彻底,在收卷部分增加冷却装置,收卷时张力不要过大。 4. 附着力差 故障现象:在印刷聚烯烃薄膜时,印迹干燥后,墨膜摩擦、揉搓和用透明胶带粘拉即脱落或部分脱落。 原因:错用不是印刷薄膜的油墨;聚烯烃表面处理度没有达到;加热不当;墨膜未干彻底或加热不够。 解决方法: ①在使用油墨时,坚持油墨专用、异类不掺的原则。 ②可自配达因水,检查薄膜的表面处理度(达因水配比见附表一)。 ③印刷对象,尤其是吸湿性大的材料保管环境不应潮湿;印刷时,要根据当时的温、湿度来调配稀释剂。 5.白化 故障现象:溶剂型的凹版油墨和橡皮凸版油墨的墨膜表面干燥时,空气中的水分渗进墨膜中,使表面产生发白。此时印品无光泽、颜色不鲜艳,似有一层雾。 原因:由于温度比较高,相对湿度比较大,而使溶剂严重失调。 解决方法:调入对比油墨树脂,沸点较高的、完全溶解树脂的真溶剂,使油墨延缓干性。 加强热力是很重要的,保持到干燥完全,在调整粘度时,注意补充足够的真溶剂,使油墨中的树脂始终保持在充分溶解状态。 6.水化 故障现象:油墨中溶剂成分发生变化,使稀的油墨产生增粘、树脂析出、胶凝化、浓度减小、转移不良、糊版等毛病,特别是图案小,墨量少的部分。 原因:由于长时间印刷,空气中的水分进入墨中,或现场有水不慎进入油墨中。 解决方法;用新墨替换旧墨;调配用中等挥发性溶剂,延缓干性;检查吹风,不要对着滚筒。 7.针孔 故障现象:印品上出现微小的小孔,特别是较大面积的实地图案上最明显。 原因:当油墨比较稀薄或透明时,油墨经涂布、刮刀刮过后,油墨呈透明薄状,能看到版子上的腐蚀底纹,印刷后,印品呈大小一致的沙眼;着墨辊磨损,传墨不均匀,油墨干得太快,将网纹转印至版上;印刷压力不够或油墨流平性欠佳。 解决方法:可采用粘度比较大的油墨或者遮盖力较强的油墨,使油墨干速减慢;调整刮刀与版简压力,也可加入一部分防针孔剂。 8.发虚和晕圈 故障现象:图案印迹不实,墨层淡薄,叫发虚。围绕着所印图案边缘有双边或呈珠状阴影,叫晕圈。 原因:由于印版辊压力不均匀,或橡皮布垫衬得不实;油墨浓度不足,太稀薄,粘度小,引起印品发虚;或由于印版辊压力过大太重,油墨粘度小,流散性大,印版上油墨过多;也有静电原因引起印品产生晕圈。 解决方法:这两种故障,都需要调整印版辊的压力使其压力均衡,同时要采用较高浓度和较大粘度的油墨。提高干燥速度,给墨量适当,就可消除。 9.刮痕 故障现象:印品的非图文部分,有一条一条的颜色线,有时在图文部分上也能看到较厚的线。 原因:总的原因是刮刀问题。油墨中有杂质,损坏刀刃,或油墨粘度太大对印版辊筒粘附性过强,这些都可以使刮刀刃出现小口,或油墨沉积在刀下干结而刮不净造成刀线问题。也有印版辊筒引起的刮刀问题。辊筒抛光加工不良,有小的抛纹,版纹过深,刮刀在其上浮动受损。有刮刀自身引起的刮痕问题。刮刀刃锋不平直,打磨中有损伤,刮刀与辊筒接触角不适当,都会出现刮痕现象。 解决方法:印刷时,印刷机最好加上油墨循环泵,油墨循环出口处加上滤网。选用较好的弹簧钢刀片,开刮刀刃口不要太小,最佳角度为20~ 23°。刮刀与版辊筒接点切线的夹角应为45°为宜,若刀片材质不佳,则须经常打磨刀片。 10.溢出 故障现象:印刷实地图案时,满版部分的油墨呈现斑点状,而且,油墨会出现从图案部分散出扩大的毛边现象。 原因:主要是油墨粘度过低,造成了流平性不好,印品不平实。由于稀薄,在比较低的印刷速度下,从刮刀刮除非图文部分的墨到压印点的时间长,在转动中油墨从网穴中散出来,在图案周围造成扩大影迹;刮刀安装的角度太小,网穴图案部分刮不净;版纹较深,盛墨多,也会造成低粘度的墨流平不好和散流于图案以外。 解决方法:油墨粘度低时,应及时更换新墨。调整时不要用大量的单一溶剂,应配以同类油墨的冲淡剂,以提高和保持油墨的较高粘度;提高印刷速度,防止形成流散;还可以改变刮刀角度,使角度变大,直对着辊筒刮去网穴中比较多的墨,防止墨层不适当的厚度;版纹过深时,一是改用比较稠的墨,二是重新做较浅的印版(暗调版纹以30~35μm为宜)。 11.桔皮状斑纹 故障现象:印品印迹不平服,特是满版实填部分,呈水纹桔皮状。水纹不露底,皮膜呈不规则的波浪形与桔子皮纹相似。 原因:主要原因是油墨的流平性不好,油墨适性太差,触变性太大。再加上油墨干性太快,粘度大,压印后分裂时辊简不圆而产生振动。在使用水溶性油墨时,由于印刷对象对油墨的排斥力太大和静电现象的影响。 解决方法:把注意力集中到保证油墨有很好的流动性方面,即“尽量保持较高粘度”,与机器适应而印刷。使粘度为20~30s(4号杯)。用流动性好的、含树脂的调整剂。使油墨初干性稍慢一些。如20~40mm/25℃。同时,调整机器压印辊上的垫衬以及有关机件使之减少振动,同时,消除静电影响。 12.墨斑 故障现象:在印刷品的暗调部分上,出现不规则,不平的丝杠、点子和隐约可见的斑块,给人以山峰状或粒状不均匀感觉。 原因:由于油墨粘度太低,印刷速度太慢,干燥又慢,油墨象水一样向一个方向流挂。也可能在高调处分布好,而在暗调处就发生斑点。 由于油墨流动性不良,又比较稠,触变性太大,流平性不好,墨量不足,容易发生斑点。采用的溶剂不是与油墨相匹配的或者是误将油墨用错,混进了不同类型的墨;使用的是重复使用而白化、水化了的油墨;用了有凝胶性质而未充分恢复的油墨;油墨对印刷体湿润能力差。还有因版深产生静电现象;压力不适,刮刀角度不合适,造成了油墨分裂流平铺展中不规则的振动。 解决方法:采用比较稠的油墨或将太稀的油墨与新墨并用;用对应的溶剂使干性加快,并且要使溶解树脂的真溶剂挥发稍慢于助溶剂。增加流动性好的调墨油成分,采用粘度大而触变性小的油墨,使其呈良好的流平性;换用与油墨相匹配的纸张或对塑料表面再处理,使油墨充分湿润其表面;改用比较浅的印版;压力稍加大,刮刀压力减小,角度变大。造就合理的印刷条件。 13.缩孔 故障现象:印品墨层或上光清漆面上出现象喷泉或火山口状的突起的斑点。有时整个图案处均有。印刷表面粗糙,光泽度降低。 原因:油墨表干太快。热力首先强烈地作用表面而形成干膜,靠下层的溶剂被暂时封闭,而继续受热时,其内溶剂要逸向外界,能量达到突破表膜的程度时,喷发出来,从而形成缩孔毛病。 解决方法:对于比较厚的印刷品墨层,平性问题一定要调整好。也就是说溶剂的挥发速度或蒸发潜热要均衡,不要差距太大。做到挥发平衡,使底部结膜迅速,溶剂残留要很少。使它们在比较低的温度时挥发大部分,再继续加热,挥发一部分,再在较低温度,挥发少部分。呈这样的温度坡度为好。改善油墨的流动性能,稍延缓其干燥性,这种现象即可消除。 (co) 14.“梨皮”状 故障现象:在套叠印中,当第二色油墨覆盖在第一色墨膜上时,第一色已形成的墨膜被其溶解,上下两层局部掺合使皮膜呈翘起状态。 原因:油墨中树脂(象聚酰胺树脂和松香脂树脂)被溶解性很好,就容易发生梨皮故障。 油墨的粘度,尤其是第二色粘度太小,相应的溶剂太多,强溶剂也就多;油墨的干性,尤其是第二色的干性太慢,溶剂浸泡第一色墨膜时间就长;印版太深,墨层就厚,其浸泡第一色油墨时间也就长。所以,第一色墨膜遭破坏的机会就多,程度会大。 解决方法:提高第二色油墨粘度,提高干性,加强热风量,促使其快砍最有效。 15.静电 故障现象:其他各种条件均正常的情况下,印品图案发生周围丝须状滋墨现象;实底部分印不整齐,有斑点,有空白的墨斑;或收卷不整齐,滑动等。这就是静电引起的。有时候无明显征候着火,是静电向附近导体激烈放电,发生火花所致。有时,静电吸附周围的尘埃,使其掺入油墨,附着在印品上形成针孔,给印刷过程带来麻烦。 原因:静电是不导电的物体,如纸,塑料薄膜等,在印刷中摩擦、接触、剥离时产生的电荷现象。 防止和消除办法:一般事先在油墨中加入防静电剂,防止墨斑或滋墨故障,但不能防止电阻高的PE、PP等本身带电。需采取下列措施:在印刷现场洒水,降低印刷现场温度、使湿度变大;对高电阻材料压印后,设法使其接触金属接地线消除静电;对机器上的导辊亦采取接地措施,由于它与机体上轴承部分的润滑油接触而绝缘;使油墨保持较高的粘度来印刷。 16.脏版 故障现象:这是在非图文部分上有一层很薄的油墨转印在承印物不应有油墨的部分。 原因:油墨中的树脂和溶剂对金属表面粘附强或是对其湿润性强。例如,使用时间长或湿度高,油墨产生静电,对铬亲和性大了。铬层出现树皮层,即整个镀层有树皮状微条纹;镀层粗糙或有不规范的麻点;刮刀角度太小或刮刀已钝而刮不净。油墨初干太慢时,遇到以上情况也会脏版。 解决办法:首先要降低油墨粘度,减少其对印版的粘附性。若是镀铬层发生问题,一要重新做版,二要使油墨加快干燥。 17.水纹 故障现象:印品实填部分有水波纹现象发生。 原因:调整过失,油墨稀落到了极点。使用粘度没有掌握好。 解决方法:不要将油墨兑得过稀,若墨槽中还有过稀的油墨,应补充一部分原墨,并检查油墨的品质,看油墨的粘度是否太低并解决。 18.重影 故障现象:油墨在叠印部分出现双影或多影现象。 原因:主要是由于压力辊压力过大或张力不均匀所致。 解决方法:调整好各印版压力辊筒的压力,调整好印刷机的张力。 19.不上版 故障现象:油墨转移性不良,印品着墨量少。 原因:稀释剂含杂质造成的,如含有水或者含有其他对油墨不溶解的物质。也有油墨制造本身的原因。 解决方法:在印刷前,预先测试一下油墨与稀释剂的混合效果,以免造成损失。 若出现不上版的现象,可用原墨上机印刷测试。 1.目的: PE和PP薄膜印刷前,要进行电晕预处理,以提高印刷适性。目前主要采用表面张力测定液,用来测定薄膜预处理后的效果,表面张力测定液配方见上表。 2.方法: 用脱脂棉球蘸上已知表面张力的测定液,涂在已被电晕处理过的薄膜上,涂布面在30mm2左右,在2s内收缩成水粒状,则薄膜电晕处理强度不足,需重新提高电晕处理强度再行冲击,若试液在2min内不发生水纹状收缩,则表明薄膜已达到处理效果。 3.指数: HDPE薄膜处理强度应≥38dy为佳。 LDPE薄膜处理强度应在38~ 40dy为佳。 PP薄膜处理强度应在38~ 40dy为佳。 PET薄膜处理强度应在42dy以上为佳。 |